A Technologist's Guide to Yarn Realization
A Few months before, The cotton spinning industry faced turmoil due to skyrocketing cotton prices, which peaked at ₹1,00,000 per candy, creating a significant price disparity of over ₹20 per kilogram with yarn. In medium-count cotton spinning mills, raw material costs account for approximately 75% of total sales revenue, making it crucial for technicians to optimize yarn realization without compromising quality, thereby enhancing profitability.
Yarn realization norms vary across spinning mills due to differences in raw material properties, such as fiber characteristics and trash percentage, which are influenced by regional variations in raw material sourcing.
Enhanced yarn realization boosts a spinning mill's competitiveness and profitability by optimizing raw material conversion into finished yarn. Key factors influencing yarn realization include Raw material usage, Blow room, cards, and combers efficiency, Waste management (sweeping, hard, overhead cleaner, gutter, top roll clearer, filter, micro dust, and invisible loss).
The value of waste generated during yarn production is significantly lower than the initial cost of cotton, highlighting the importance of efficient yarn realization. Currently, spinning mills achieve 85-95% yarn realization for carded quality, 68-70% yarn realization for comber quality.
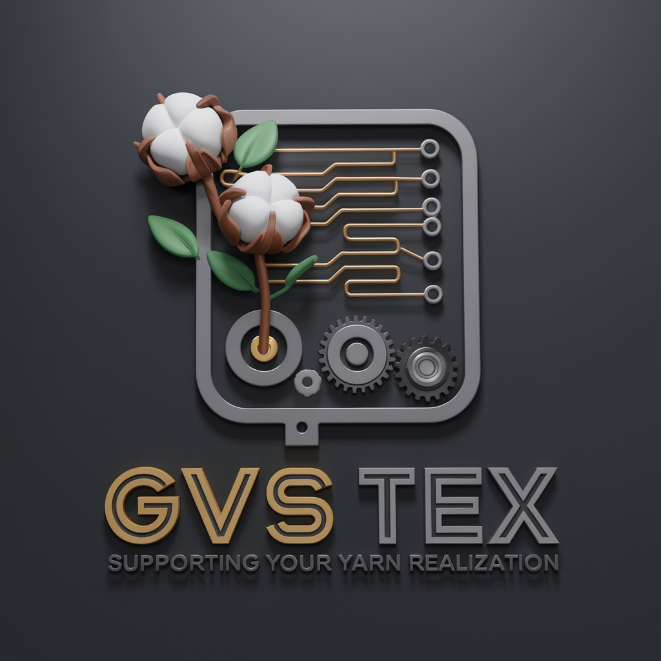